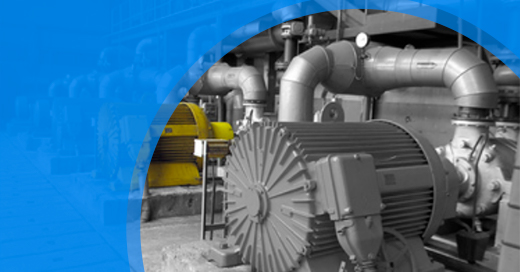
STA – Synchronous Time Averaging – How to isolate one machinery from the workshop vibration?
How to eliminate unwanted noise and vibration from the measurement environment?
Noise and vibrations propagate throughout their environment and are difficult to eliminate. In the field – in vehicles and factories, for instance – many unwanted sources can affect the signature of the targeted unit under test while it is being measured. Synchronous averaging, in the time or angular domain, is able to reject all signals that are not correlated with the cycles or excitation of the targeted unit.
How synchronous averaging isolates and cleans the signature of the unit under test?
Time-to-frequency transformation using FFT buries the spectral result with a large standard deviation which can be reduced by averaging. This averaging can be done at four different steps of the FFT/SOA process:
- The most common, Frequency/Order-domain Averaging (FA, OA), averages the amplitude spectra. The entire amplitude frequency distribution is displayed. The average count is 3 to 5 to remove the standard deviation.
- Synchronous Time-domain Averaging (STA) starts time domain block acquisition synchronously with the unit-under-test cycles. Typically, this is one pulse/rev for rotating machinery or an impact threshold for bump-tests. Since asynchronous waves are out of phase, repetitive averaging cancels out their positive and negative amplitudes. The synchronous waves (same phases) are maintained and smoothed to provide a clean, unique time block. As a result, FFT provides a standard deviation-free, complex spectrum/FRF of the unit-under-test signature. The average count is 30 to 50 times.
- The Synchronous Angular-domain Averaging (SAA) method is derived from STA. It applies in the angular domain using Synchronous Order Analysis (SOA) resampling for variable-speed machinery. It provides order spectra/profiles with better elimination of unwanted signals. STA and SAA benefit from the high-accuracy Synch inputs to synchronize the samples down to 1/64th of the (re-)sampling.
- Frequency Domain Synchronous Averaging (FDSA) uses the phase of one frequency from the measurement to synchronize. The averaging applies in the complex frequency domain with a phase shift. FDSA features synchronizing from a vibration or noise instead of the time domain edge.
Why synchronous averaging improves measurement quality?
Synchronous averaging is the best solution to clean and isolate the targeted measurements with various applications:
- Health check of rotating machinery in a workshop: using STA to isolate the vibration of one steady-state machine eliminates the unwanted vibrations from the other units in the workshop.
- Extraction of the background spectrum on operating machinery with a bump test: using STA synchronized with the impact edge of a bump test provides structural dynamics spectra without the operating vibrations of the machinery.
- In-vehicle sub-systems: the noise and vibration signature of cars, trains, ships and aircraft. These units operate at variable speed; the SAA method manages these variations to prevent them affecting results and to reject all asynchronous signals from the unit-under-test environments.
- Industrial fan diagnostics, without access to the fan cycles: FDSA can be used on the fan first order with a simple microphone to isolate the vibrations from the fan.
Rotating machines vibration analysis - 3 secret tricks to isolate your vibration signals
Download this whitepaper to find out even more on STA – Synchronous Time Averaging. (please be logged in my.oros or just create an account)
Application-oriented solutions
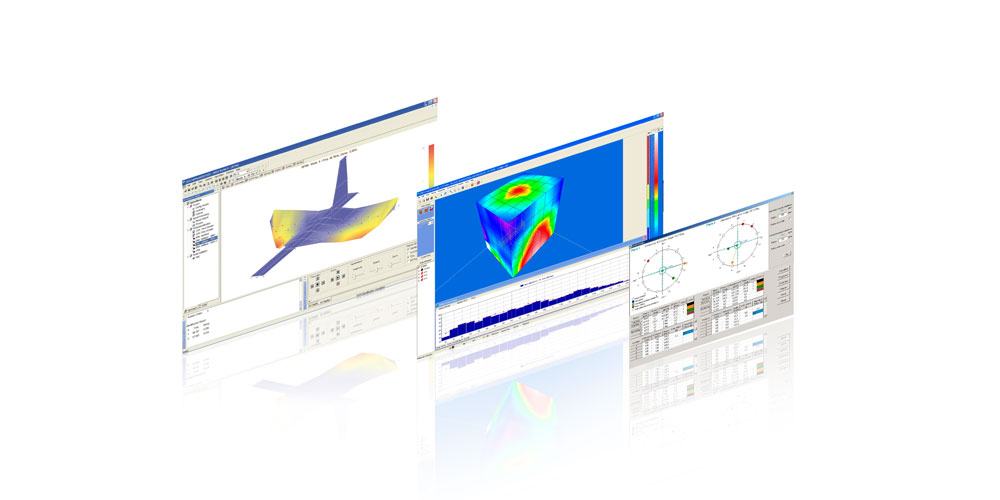
Software suite
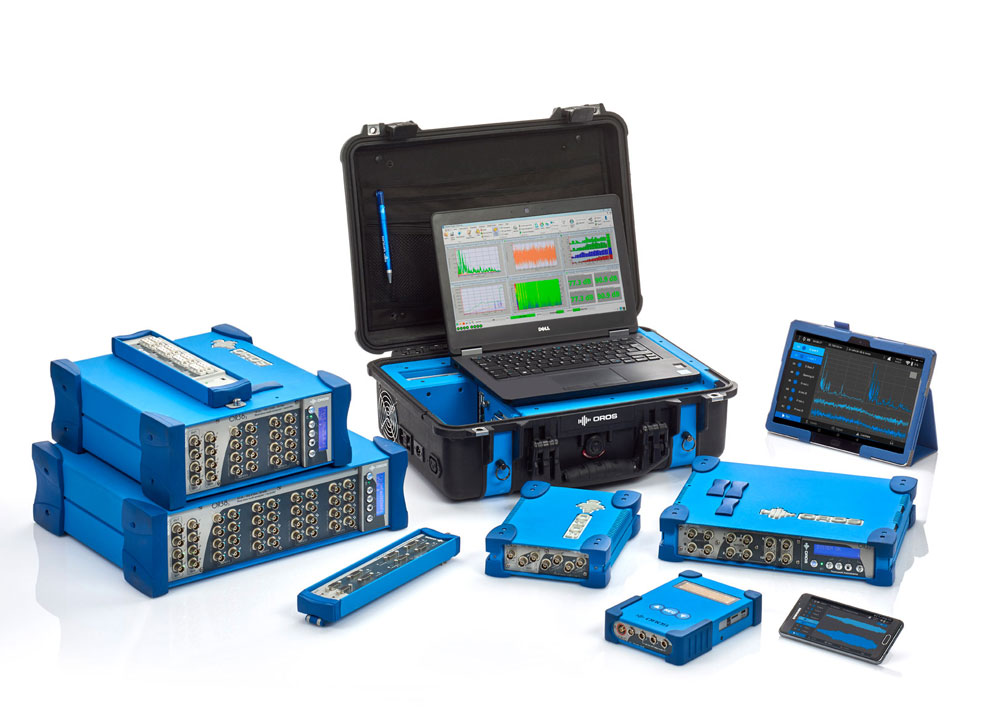
Systems and accessories
- 2 to 32 channels / system; can be cascaded and distributed up to 1000 channels
- Online & offline
- Handling any transducers
- Rugged and portable
- Stand-alone & remote monitoring modes
- Easy integration for test benches
Discover the full range of OROS noise and vibration instruments.